In the world of 3D printing, innovation isn’t limited to gadgets or toys—it’s also transforming how we approach structural components. One of the most interesting and practical applications is the 3D printed angle iron. Traditionally made from steel or aluminium, angle irons provide right-angle structural support in shelving, furniture, framing, and DIY builds. With 3D printing, hobbyists and engineers alike are now crafting custom, lightweight, and cost-effective versions of these components using durable polymers.
This article explores the design, printing, and use cases of 3D printed angle irons. We’ll break down how they compare to metal versions, the best materials to use, and tips for maximising strength and usability.
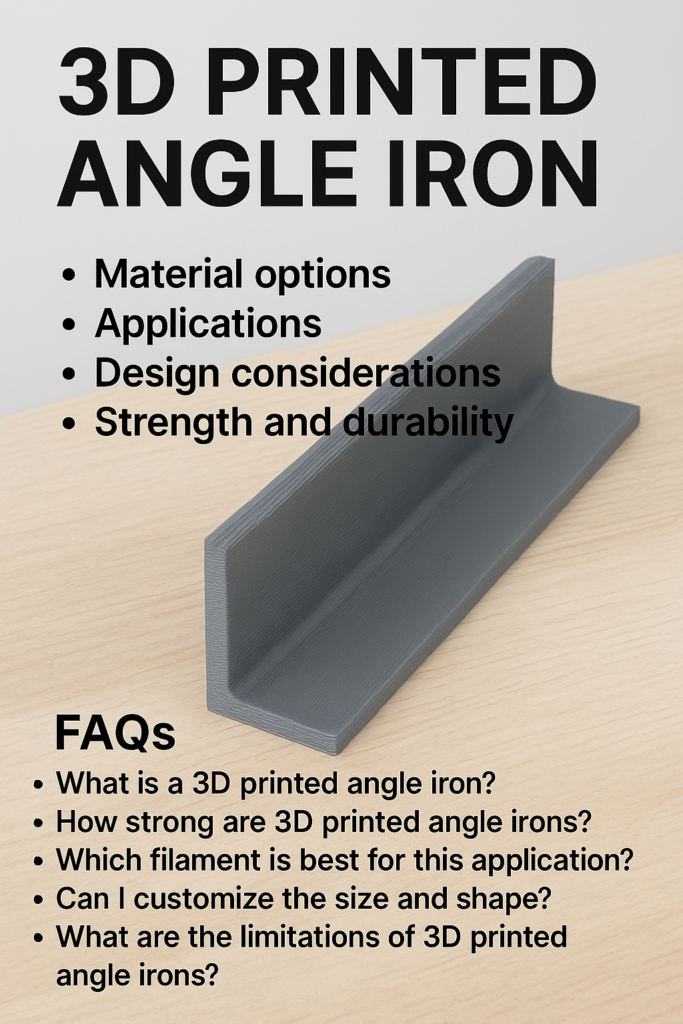
What Is a 3D Printed Angle Iron?
A 3D printed angle iron is a right-angle bracket fabricated using additive manufacturing methods. These components can mimic traditional metal angle irons but are often used in lower-load or specialty environments.
They are commonly used for:
- DIY shelving and racks
- Lightweight frames for electronics or furniture
- Bracing in 3D printed enclosures
- Robotics and prototyping structures
The greatest advantage? Customization. You can tailor dimensions, hole spacing, and wall thickness according to your exact needs.
Why Choose 3D Printed Angle Irons?
Here’s why more makers are switching to printable options:
- Custom sizing: Fit exact dimensions for your specific build
- Lightweight: Ideal where metal strength isn’t needed
- Non-conductive: Safer for use around electronics
- Affordable: Saves on cost compared to aluminum or steel
- Quick Prototyping: Rapid iteration for design testing
They’re not intended to replace metal in high-stress areas but are ideal for functional prototypes and low-weight applications.
Materials: What to Print With
Material choice affects durability. Here are the best filament options:
- PLA+ (Tough PLA): Easy to print, good for light-duty brackets
- PETG: Offers greater strength and heat resistance
- ABS: Impact-resistant but prone to warping unless enclosed
- Nylon: Excellent strength and flexibility, but challenging to print
- Carbon-fiber-infused filaments: For enhanced rigidity and durability
Best Overall Pick: PETG for ease of printing and improved mechanical strength
Design Considerations
When designing or selecting an STL file:
- Use triangular or gusseted supports for additional strength
- Add countersunk holes or recessed slots for fasteners
- Set wall thickness to 2.4 mm or more (3+ walls)
- Consider infill patterns like Gyroid or Grid at 40–60% for strength
- Include ribs or thicker junctions to reduce stress cracking
Design your model using Fusion 360, Tinkercad, or Freecad for complete control over dimensions and structural support.
Print Settings for Functional Strength
Getting strong prints means tweaking your slicer settings properly:
- Layer height: 0.2 mm for structural parts
- Infill: 50% or higher
- Walls: 3–5 for strength
- Nozzle temp: Based on filament (e.g., 240°C for PETG)
- Bed temp: 70–90°C for PETG, 60°C for PLA
- Print speed: 40–50 mm/s
- Cooling: Turn off or reduce for PETG to improve adhesion
Printing slower and hotter will yield better inter-layer bonding, which is essential for strength.
Mounting and Post-Processing Tips
To ensure your printed angle iron performs well:
- Use flat head screws and washers to distribute stress
- Drill out or ream holes for precise fits
- Consider adding epoxy coating for increased strength
- Sand mounting edges to remove burrs or uneven layers
- You can also reinforce your print with embedded metal rods or epoxy resin infill for added load capacity.
Real-World Use Cases
3D printed angle irons are more than prototypes. They can be used in:
- Camera rigging frames
- IoT enclosures and mounts
- Tool holders and shelving brackets
- RC vehicle frames
- Repairing lightweight furniture
- Educational robotics
Because of their modularity and low cost, they are great for temporary or evolving setups.
Limitations and When to Use Metal Instead
- Not suitable for heavy loads
- Weaker in high-temperature environments
- Can wear out under vibration or stress over time
If the application is structural or critical, like in construction, traditional metal hardware is still the safer choice.
READ MORE – 3d Print Torx 25 Router Plate: DIY Stability and Precision for Makers
FAQs:
1. Can a 3D printed angle iron hold real weight?
Yes, within limits. With PETG or carbon-fiber PLA and thick walls, they can support light to medium loads.
2. What’s the best design for maximum strength?
Use gussets, thick walls, and a high infill percentage. Avoid sharp inside corners.
3. Can I use a 3D printed bracket outside?
Yes, if printed with UV-resistant filament like ASA or weatherproof PETG.
4. Are these safe for electrical projects?
Yes, they’re non-conductive and safe near electronics.
5. How do I reinforce a printed angle bracket?
Add embedded rods, use epoxy infill, or double up the design for redundancy.
Conclusion:
The 3d-printed angle iron is a powerful example of how additive manufacturing is reshaping basic hardware. For light-duty applications, design experimentation, or DIY creativity, 3d printed brackets offer cost-effective versatility and surprising strength when printed correctly.
With the right filament and design strategy, your angle iron can be more than just a plastic piece; it can be a customised solution that fits your needs exactly.